With all my respect I have to differ in many points. I have to poit out that I have no issues with you personally - moreover I really value that you are an active and helpful member of the forum - but I hate when the same misconceptions are repeated over and over.
waspmike wrote:The O2 sensor only works during certain times based on input parameters. I believe they are not used during WOT?
The O2 sensor works all the time. It is a simple, single wire zirconia type passive element without a heater or a charge pump. It will generate an output voltage based on a chemical reaction between two zirconia plated ceramic elements in presence of oxygen. As I wrote earlier it has a switching type characteristics, practically having a very steep change curve of 10V/sec to indicate it the exhaust gases are richer or leaner than the preset 14.7 AFR value.
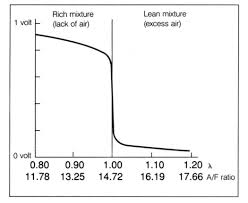
- Zirconia O2sensor voltage.jpg (5.91 KiB) Viewed 11151 times
This is why the AFR is actually fluctuating at idle and cruise as the ECU cannot set AFR exactly at that working point but continuously overcompensating slightly around the value.
The only input parameter for the O2 sesor is the gas it measures. It is however very sensitive to heat, below 600 deg C it is not providing any useful info, that's why it is placed in the head to keep it up to temperature.
It's signal is neglected by the ECU at WOT.
waspmike wrote:Injectors are HP rated, not flow rated. What injector you used depends on what HP you have.
Please, please don't say this again, because I'll start creaming. I already get cranked when the injectors are described as "6 hole large injector" for instance. It is certainly helps to identify them in one' parts box or drawer, but have nothing to do with the capacity of the unit. Only uneducated shadetree trial-and-error backyard mechanics (or in fact parts guys working with them) would call an injector HP rated - as it is
completely false.
A given injector will not change the HP of an engine, therefore it cannot be identified or rated by that. There are many parameters to describe an injector (like maximum duty cycle, max operation pressure, flow rare, impedance, drive circuit type etc.) - but HP is not of them. The only parameter that can practically enable comparing two injectors is flow rate per time unit at a given pressure (usually cc/sec, grams/min or lbs/hour on 2 or 3 bars). Maximum HP rating is specific to an application (overall engine efficiency with the maximum fuel delivered at an RPM) and not to an injector.
Let me just use the example of BPT's case right above. He is currently using a larger injector than he should in his current setup. During the closed loop operation the injector hasn't changed the horsepower of the engine, as it is compensating the extra flow by providing shorter injection time. In the open loop portion where due to lack of usable feedback from the O2 sensor the injection times are fixed it dumps way more fuel than needed - therefore actually he gets less power than he could with a properly sized setup.
Also an undersized injector might not be deliver enough fuel even at 10% duty cycle at high RPM therefore limit reachable HP, but then in the automotive tuning industry it is very common to use variable rate fuel pressure regulators, and with increased pressure it might easily deliver 20 or even 40% more fuel - resulting in more HP.
On the other hand if BPT would have the right information on injector flow rate and could select the right injector to his application, he could for example select a proper injector what delivers exactly 20% (150-125)/125=20%) more fuel than the factory one and would be more or less spot on with his fueling at WOT.
I hope it is clear now why it is understandable why it important to use the right measures when planning to work on an engine.
waspmike wrote:A piggy back unit will adjust the fuel of course.
Not all piggybacks are altering fueling directly. In fact it directly adjusting fueling may not work at all in certain applications.
As I wrote above during closed loop operation the ecu compensates for any deviation from it's set working point. Therefore it is completely useless and would lead to inconsistent fueling to adjust fueling directly. In this part of the operation the only way to have a consistent solution with a piggyback is to alter the O2 signal feedback to the ECU. As the narrowband (NB) sensor will not be able to detect such conditions a wideband (WB) sensor is needed with the proper programming. The easiest solution is to have a WB contoller installed and change the switchover point set to a different AFR - eg. 13,5. This way the feedback is still working towards the ECU and it will control the operation by adjusting fueling to the new setting. It is very important, as the ECU has the extra sensors (e.g. cylinder head temp, intake air temp, manifold absolute pressure and ambient air pressure) to be able to compensate for other minor external factors which are not cared for by a piggyback controller.
Outside of the closed loop operation envelope it is true though that the only way to alter fueling is to directly modify injection length to deliver more or less fuel than the factory preset values would allow.
waspmike wrote:Don't forget that in three stage units like Two brother Juice box (made by Dobeck) the three stages are Cruise, Acceleration and Full throttle.
Regardless of whether you have more stages in say a PC based system, for a CVT scooter there are only effectively two stages. Cruise and full throttle. There is no "Acceleration" phase in which one has relatively low RPM vs high throttle opening as would be the case with a motorbike. This is of course because the CVT changes gear during acceleration so there is no low RPM vs high throttle opening.
Generalization, what does not seem to hold firmly. I have made quite long data logging sessions before started modifying my bike and found that 5-15% of my riding is in fact in slow acceleration, or mid load phase. These are typically around mid speed (30-45miles, or 40-70km/h) where I either only have to accelerate slowly or going slightly uphill and the engine is under increased load but the variator does not change gears.
Therefore I would not rule out using a properly set up fuel controller for acceleration stage either.
waspmike wrote:Piggy back fuel controllers will not add speed or performance to stock bikes. Most motorcycle ECUs have enough capacity in them to allow for aftermarket exhausts.
This is also a common misconception, and also a generalization as different piggybacks are working differently, therefore not necessary true.
First of all in case the top speed is limited by power (the engine does not hit the rev limiter at top speed which is the case with the 125 on level road) actually increasing the power output at the top RPM range will change top speed AND acceleration.
Let me cite a dyno chart from Akrapovic. It shows charts of both the stock and an aftermarket exhaust - no other changes and fueling is still stock and provided without any adjustments. One can see, that this simple change will effectively change the top end power curve of the bike, effectively raising the top speed reachable.
How it works. As the variator cannot adjust to spin the engine at the RPM with max power at all times (it will lock out at a point and from there any increase of speed can be only reached by raising the engine revolutions) on less powerful bikes the max speed will be reached before hitting the rev limiter as at that point the engine is not able to provide enough power to accelerate further. If high revs power is raised - the flat road top speed will be raised also as the bike will accelerate further with more power available. On the attached dyno chart one can see also, that 0-100km/h accelaretion is shorther by 1 second (down to 15 from 16) which might not be a lot - but it is a change. If fuel would be compensated to the increased flow - even more changes could be realized as we have discussed that stock ECUs are not compensating for fuel in open loop mode.
Second. Most fuel controllers are able to raise the rev limiter, so in case the top speed is limited by the rev limiter and the transmission gearing (like it is on a PCX150 on a level road, or on a 125 on a downhill) an increase from 9.500 to 10.000 RPM can actually raise the top speed even on an otherwise stock scooter.
Now if the second rev limit raising version is healthy or not on a stock engine - is a different question - but it is definitely able to change top speed and performance.